Искусство шить
05.10.2018
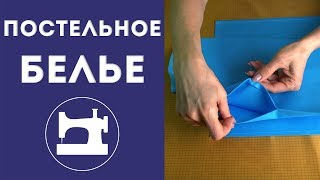
Записи с меткой "лекала"
На детали одношовного рукава долевая проходит параллельно линии середины рукава (рис.а).
Если линия середины рукава не обозначена, ее можно найти проведя перпендикуляр через середину отрезка 1-2
На деталях двухшовного рукава долевая проходит параллельно линии, соединяющей концы переднего среза, т.е. параллельно линии 3-4 на верхней части рукава и 5-6 на нижней части рукава (рис.б).
Как научиться шить с нуля? Школа шитья Юли Балль
Если вы хотите знать, как должна проходить долевая на всех других деталях одежды, вам будет полезен курс «Долевая в одежде и деталях кроя», подробнее об этом можно узнать здесь
Код работы | Содержание работы | Код непосредственно предшествующих работ |
1 | Разработка и утверждение технического задания на изготовление новой модели | |
2 | Разработка конструкции модели, включающей измерение модели по основным параметрам, подбор основы, внесение конструктивных модельных особенностей и подбор унифицированных деталей | 1 |
3 | Построение и изготовление лекал модели среднего размера и роста, построение лекал подкладки, бортовой прокладки, вспомогательных лекал, проверка и уточнение сопряжения срезов узлов и деталей по всем линиям | 2 |
4 | Определение экономичности первичной конструкции с учетом таблицы интервалов площади лекал | 2,3 |
5 | Внесение изменений в лекала для нахождения оптимальной площади лекал | 4 |
6 | Раскладка, зарисовка лекал и раскрой первичной конструкции | 5 |
7 | Изготовление первичного образца конструкции | 6 |
8 | Примерка готового образца, Уточнение внешнего вида, посадки на фигуре, технологии, использования материалов, фурнитуры и т.д. | 7 |
9 | Анализ первичной конструкции, проверка ее параметров по табелю мер, проверка и уточнение лекал деталей из основной ткани, подкладки, вспомогательных лекал. Уточнение технических описаний | 6,7,8 |
10 | Определение экономичности конструкции после внесения уточнений | 9 |
11 | Раскрой опытной партии изделий | 10 |
12 | Изготовление опытной партии изделий в потоке | 11 |
13 | Просмотр и утверждение опытной партии | 12 |
14 | Изготовление экспериментальной раскладки | 13 |
15 | Градация лекал | 14 |
16 | Проверка лекал после градации | 15 |
17 | Изготовление лекал-эталонов и рабочих лекал | 16 |
18 | Нормирование сырья | 13,14 |
19 | Составление технической документации | 17,18 |
20 | Калькуляция и определение рентабельности изготовления новой модели | 19 |
21 | Согласование с отделом труда и заработной платы | 19,20 |
22 | Согласование с плановым отделом | 21 |
23 | Утверждение технической документации перед запуском в производство | 19,20,21,22 |
24 | Запуск модели в производство | 23 |
Конструкторская документация на новую конкретную модель оформляется в виде технического описания с приложением комплекта лекал деталей из основной ткани, подкладки и приклада. Далее...
Градация или техническое размножение лекал – это получение комплекта лекал всех размеров и ростов соответствующей полнотной или возрастной группы по лекалам деталей изделия среднего размеророста.
Известны три способа технического размножения лекал: группировки, лучевой и пропорционально-расчетный.
Способ группировки сводится к получению лекал деталей одежды различных размеров в результате совмещения двух комплектов лекал (среднего и крайнего размеров). После совмещения лекал одноименные конструктивные точки соединяют прямыми линиями. Эти линии делят на число частей, соответствующих числу промежуточных размеров.
Основной недостаток способа группировки заключается в том, что необходимо строить чертежи не на один, а на два размера. Этот способ используют как исходный для нахождения величин приращений в основных конструктивных точках типовых схем технического размножения лекал, используемых при других способах, а так же при размножении лекал деталей одежды сложных моделей.Сущность лучевого способа состоит в том, что из определенной точки (фокуса) через все конструктивные точки проводят прямые линии (лучи). От контура детали вдоль этих лучей откладывают величины приращений. По вновь найденным точкам вычерчивают контуры деталей больших и меньших размеров.
Этот способ наиболее простой, но наименее точный. На точность его влияет в первую очередь выбор положения исходной точки (фокуса). При разных положениях фокуса направление лучей получается разным, конструктивные точки лекал смещаются, а контуры их искажаются. Лучевой способ может быть использован при размножении лекал отдельных деталей головных уборов и корсетных изделий, приращения размеров которых происходят в радиальном направлении.
Наиболее широкое распространение при конструировании получил пропорционально-расчетный способ размножения лекал . Сущность этого способа состоит в том, что конструктивные точки лекал перемещают по горизонталям и вертикалям с учетом соответствующих приращений лекал по горизонтальным и вертикальным осям в соответствии с изменениями размерных признаков тела человека и положением линий членения.
Величины приращений по горизонталям и вертикалям для каждой конструктивной точки лекал находят, исходя из определенного положения точки относительно исходных (нулевых) линий (осей). Для основных деталей плечевых изделий принимается следующее расположение исходных линий.
На спинке вертикальная линия совпадает с серединой спинки или линией, касательной к средней линии спинки, горизонтальная – с линией груди (глубины проймы) или линией талии. На полочке вертикальная линия проходит касательно к линии проймы, горизонтальная – совпадает с линией груди (глубины проймы) или линией талии.Лекала разрабатывают основные, производные и вспомогательные.
К основным лекалам относят лекала деталей из основного материала: полочки, спинки, верхней и нижней частей рукава, нижнего воротника, переднего и заднего полотнищ юбок, передней и задней половинок брюк т.п.
К производным лекалам относят лекала деталей изделия, служащие для обработки краев деталей (подборта, обтачки, верхний воротник, пояс юбки и брюк и др.); лекала функционально-декоративных и декоративных деталей и элементов модели (клапаны, листочки, накладные карманы, хлястики и т.п.); лекала деталей из подкладочных материалов (лекала подкладки спинки и полочки, верхней и нижней частей рукава, юбки, жилета и т.п.); лекала деталей из прокладочного материала (лекала прокладки в воротник, в борта полочек и т.п.) и лекала из дублирующего прокладочного материала ( лекала дублирующей прокладки в полочку пиджака и др.).
Производные лекала строят по основным лекалам.К вспомогательным лекалам относят лекала для разметки мест расположения карманов, вытачек, складок, петель и пуговиц, для подрезки лацкана и борта, низа изделия, нижнего воротника и др.
В состав технической документации на модель одежды входят лекала – оригиналы и лекала-эталоны .
Лекала-оригиналы – это лекала, полностью соответствующие подлинному образцу модели изделия на базовый размер и предназначенные для выполнения размножения лекал.
Лекала-эталоны – это лекала, полученные по лекалам-оригиналам путем градации на все размеры и роста рекомендованной полнотно-возрастной группы и предназначенные для изготовления образцов-эталонов швейных изделий и для проверки точности и качества рабочих лекал.
Рабочие лекала – это лекала, изготовленные по лекалам-эталонам и предназначенные для выполнения раскладок, их зарисовки или изготовления трафаретов и для проверки качества кроя.
Технические требования к изготовлению лекал.
Перед построением лекал на чертежах конструкции деталей изделия все тупые углы вытачек, линий боковых швов, средней линии спинки, линий рукавов скругляют с возможно меньшим отклонением от их вершин. Затем проверяют сопряжение деталей полочек и спинки, верхней и нижней частей рукава в местах их соединения по линиям швов с минимальным отклонением от конструктивных линий.
По чертежам конструкции изделия изготовляют основные и производные лекала-оригиналы, в которых учитывают припуски на швы и подгиб. После технического размножения этих лекал изготавливают основные, производные и вспомогательные (подсобные) лекала-эталоны и рабочие лекала всех размеров и ростов.
При построении лекал для изготовления швейных изделий в условиях массового производства одежды используют нормативно-техническую документацию.Технические требования к оформлению лекал.
На основных и производных лекалах согласно техническим требованиям на раскрой деталей изделия наносят следующие обозначения:
линию долевого направления ткани – направление нити основы (н.о.); линии допускаемого отклонения от долевого направления; линии минимальной и максимальной ширины надставок в местах их расположения согласно отраслевым стандартам на изделия; контрольные надсечки для совмещения деталей при их соединении.На вспомогательных (подсобных) лекалах наносят места расположения карманов, вытачек, складок, петель, пуговиц и т.п.
По линиям срезов всего комплекта основных, производных и вспомогательных лекал-эталонов и рабочих лекал на расстоянии 1мм от края ставят клеймо через каждые 8-10 см или проводят линию для контроля степени износа рабочих лекал.
На лекало каждой детали наносят маркировочные данные: наименование изделия, номер модели, типоразмеророст, наименование детали, шифр (при использовании унифицированных деталей), площадь детали, количество деталей кроя.
Весь комплект основных, производных и вспомогательных рабочих лекал должен быть проверен отделом технического контроля и иметь дату, подпись, штамп ОТК. Проверка рабочих лекал, находящихся в производстве, осуществляется по лекалам-эталонам и табелю мер не реже одного раза в месяц.
Для установления неточностей в размерах вследствие деформации картона лекала-эталоны проверяют по табелю мер не реже одного раза в квартал. После каждой проверки на лекалах ставят дату, подпись и штамп ОТК
Построение раскладок в компьютере, зарисовка их в натуральную величину или раскрой на АРУ – именно ради решения этой задачи создавались первые швейные САПР. Автоматическая, быстрая, предельно плотная раскладка лекал – давняя мечта изготовителей одежды, так как от качества раскладок зависит себестоимость и конкурентоспособность производимых изделий.
Многолетний опыт использование САПР раскладки на предприятиях убедительно показал значительные преимущества компьютерных технологий формирования раскладок перед традиционным ручным способом.
Применение САПР для проектирования раскладок:* обеспечивает экономию сырья до 3 % за счет нормирования межлекальных отходов, уплотнения раскладок и устранения потерь, связанных с обмеловкой лекал;
* повышает производительность и качество труда оператора-раскладчика, при этом напряженность труда раскладчика снижается, так как система подстраховывает и предостерегает его от ошибок; * способствует более рациональному использованию производственных площадей, так как позволяет заменить столы для раскладок лекал на компактные автоматизированные рабочие места (АРМ) и исключить оборудование для измерения площади лекал, для изготовления копий раскладок, для изготовления и хранения лекал (сокращение затрат на лекальное хозяйство составляет 75…85%); * при использовании плоттера позволяет получать зарисовки раскладок в натуральную величину в неограниченном количестве и в кратчайшие сроки; * обеспечивает условия для раскроя на АРУ (автоматизированных раскройных установках).Процесс формирования раскладки в САПР заключается в размещении изображений лекал на экране дисплея в площади прямоугольника, длина и ширина которого соответствуют параметрам полотна настила.
Существует три основных режима формирования раскладок.
* Ручной или диалоговый — когда очередность и местоположение лекал выбирает раскладчик.
* Автоматический — когда система сама строит различные варианты раскладок и выбирает лучший. * Полуавтоматический или комбинированный — когда часть лекал раскладчик укладывает по своему усмотрению, а остальные — система.Рассмотрим каждый из этих режимов подробнее.
* Ручной (диалоговый) режим формирования раскладок лекал
В ручном режиме раскладчик лекал выполняет на экране компьютера практически ту же работу, что и на столе.
Оператор-раскладчик на экране дисплея выбирает и помещает нужные лекала в поле раскладки. Система фиксирует лекало в указанном месте и автоматически выполняет контроль соблюдения технологических требованиям: соблюдение заданных технологических зазоров; отсутствие пересечения внешнего контура устанавливаемого лекала с контурами ранее уложенных лекал, с границами настила, с линиями стыковки секций настила. При невыполнении любого из перечисленных требований система не допускает размещения лекала в указанном месте, подает звуковой сигнал о необходимости корректировки в размещении лекала или автоматически осуществляет корректировку расположения лекала в схеме раскладки.Качество и скорость выполнения раскладки зависит от мастерства раскладчика и удобства пользовательского интерфейса программы. В этом режиме затрачивается больше времени, чем в других режимах, но в 1,5—2 раза быстрее, чем при работе на столе.
* Автоматический режим формирования раскладок лекал
Автоматическая раскладка сложна в ее программной и технической реализации. Наличие автоматического режима раскладки лекал в САПР является свидетельством высокого профессионального уровня специалистов разработчиков системы.
При автоматическом режиме раскладки функции оператора сводятся к заданию параметров материала и выбору комплектов для раскладки, а система сама строит различные варианты раскладок с учетом заданных технологических ограничений. Программа останавливается либо по указанию пользователя, либо по истечении заданного на поиск раскладки интервала времени, либо при достижении определенного процента межлекальных выпадов. Далее система предлагает один или несколько наилучших вариантов.
Этот способ является наиболее быстрым и удобным, но, тем не менее, автоматический режим раскладки лекал есть далеко не во всех САПР, и даже при его наличии в системе им не всегда пользуются на предприятиях.
Проблема состоит в том, что ни одна автоматическая раскладка не может превзойти опытного раскладчика. Как правило, автоматическая раскладка менее экономична на 2-4 % по сравнению с ручной. Задача максимально плотного размещения плоских фигур произвольной конфигурации внутри прямоугольной области с переменной длиной одной из сторон решается только методом последовательного перебора вариантов. Но число возможных вариантов слишком велико. Например, количество вариантов раскладки для комплекта всего лишь из 5 разных деталей при соблюдении направления ворса равно 260, для того же комплекта без соблюдения направления ворса — 520, а с учетом возможных поворотов лекал на малые углы (в пределах допустимого отклонения от заданного направления долевой) их количество возрастает практически до бесконечности. Ввиду сложности задачи и многовариантности возможных решений технически затруднительно обеспечение всех требований, предъявляемых к рациональным раскладкам. Поэтому автоматические раскладки ограничены определенными условиями и не гарантируют выполнения всех требований. Так, например, автоматическая раскладка во многих САПР не обеспечивает совмещения деталей с рисунком ткани, не предусматривает использования допустимых отклонений от долевой, кромки ткани, не позволяет изменять величину технологического зазора между деталями в раскладке. Только в последние годы появились программы, обеспечивающие получение «хороших» результатов раскладки за сравнительно короткий промежуток времени.
Автоматическая раскладка не гарантируют получение оптимального, т.е. наилучшего из всех возможных, результата. Поэтому на современном этапе наиболее рациональным видится использование комбинированных программ построения раскладки, когда кроме автоматического режима проектирования, есть и полуавтоматической, в котором человек имеет возможность корректировать результат автоматической раскладки, а также изменять расположение лекал для учета специфических технологических ограничений
* Полуавтоматический (комбинированный) режим формирования раскладки лекал
Он совмещает в себе ручной и автоматический режимы. Это наиболее эффективный режим построений раскладок, так как позволяет использовать опыт оператора-раскладчика и быстродействие компьютера. Вместе они быстрее строят экономичную и технологичную раскладку, чем каждый из них в отдельности.
Полуавтоматический режим раскладки может быть реализован двумя способами:
— оператор-раскладчик вручную размещает на материале часть лекал (как правило, наиболее крупных или наиболее сложной конфигурации), затем остальные лекала раскладываются системой автоматически.
— вначале все лекала раскладываются в автоматическом режиме, а затем получившиеся раскладки просматриваются оператором-раскладчиком и при необходимости корректируются.
В некоторых САПР, например в САПР «Грация», при формировании раскладки возможен неоднократный переход от ручного режима к автоматическому и наоборот.
Эффективная программа построения экономичных и технологичных раскладок:
— поддерживает сочетание ручного, автоматического и полуавтоматического режимов с учетом различной лицевой поверхности (с направленным ворсом или оттенком, рисунком) материала, способа настилания, дефектов и технологических ограничений;
— предоставляет оператору возможность задавать дополнительный припуск к деталям (на усадку, подгонку рисунка и т. п.); объединять лекала в группу, которая будет двигаться как единое целое (это удобно для мелких, компактно уложенных лекал); зеркально отображать и поворачивать лекала; разрезать детали в любом месте на части с припуском на шов (в целях рационального размещения лекал в раскладке) и соединять части лекала в целое;
— автоматически отслеживает изменений в лекалах;
— рассчитывает наилучшее сочетание размеров и ростов моделей в одной раскладке;
— предоставляет возможность отмены операций, выполняемых в процессе раскладки;
— готовит процесс раскроя, определяя стартовые точки, направление вырезания, и т.п.
— позволяет передавать информацию о раскладке в другие системы;
— стимулирует проектирование раскладок самими конструкторами, что создает условия для корректировки конструкции модели с целью достижения максимального использования материала без снижения качества изделия;
— обеспечивает экономию времени и материалов.
Печать готовых раскладок.
Готовые раскладки записываются в файл (для дальнейшего использования) и распечатываются в натуральную величину на плоттере. Печать осуществляется на плоттере: целиком или по частям, в зависимости от формата плоттера. Напечатанная на бумаге в натуральную величину раскладка используется в качестве разметки (намеловки) при раскрое настила. На основе раскладки может быть подготовлена программа порезки настила на Автоматизированной Раскройной Установке зарубежного или отечественного производства.
Подсистема САПР «Раскладка» имеется практически во всех швейных САПР. Среди профессиональных швейных САПР пользующихся наибольшим спросом на отечественном рынке можно выделить САПР «Грация», «Ассоль», «Комтенс», «JULIVI», «Автокрой», а также «Леко», «Силуэт», «Абрис» и др.
Используются также САПР зарубежных разработчиков: Investronica Sistemas (Испания); Gerber Garment Technology (США); Lectra Sistemes (Франция); Pfaff и Grafts (Германия); AMF Sybrid (Великобритания) и др.
Список источников информации:
http://window.edu.ru Сурикова Г.И., Сурикова М.В., Сурикова О.В. Проектирование раскладок лекал деталей одежды в САПР: Учебное пособие Иваново: ИГТА, 2005.
http://www.lpb.ru Ещенко В., Светиков В., Ещенко А. Комплексная автоматизация швейных предприятий http://www.saprgrazia.com http;//www.comtense.ru http://www.autokroy.ru http://www.julivi.com Андреева М. В.,. Холина Т. Ю., Павлов А. М. Раскладка лекал в САПР «Ассоль».// Швейн.пром-сть.№4.2001В раскладках лекал деталей головных уборов, корсетных изделий, деталей кожгалантереи, обуви, мягкой игрушки используется от 10 до 300 деталей различной конфигурации и размеров, однако межлекальные отходы в раскладках этих изделий еще велики и составляют 10— 40%.
Проведен анализ деталей по конфигурации и частоте встречаемости их в раскладке. Установлено, что при всем многообразии моделей указанных изделий все детали можно объединить в конструктивно подобные группы, а в зависимости от объема выпускаемых моделей определить частоту встречаемости деталей в раскладках.
Например, с целью классификации деталей бюстгальтеров по конфигурации и частоте встречаемости их в раскладках специалисты изучили 700 различных деталей, встречающихся в 180 моделях бюстгальтеров (общий выпуск этих моделей составляет более 40 млн изделий). Установлено, что среди выделенных 59 деталей различной конфигурации в реальных раскладках наиболее часто встречаются детали только 21 подгруппы, причем они составляют более 80% общего числа раскраиваемых изделий.
На основе полученных результатов разработаны конфигурационные таблицы, содержащие детали бюстгальтеров, чаще всего используемые в реальных раскладках.
Аналогичные конфигурационные таблицы разработаны для деталей головных уборов, мягкой игрушки и других изделий.В существующей нормативно-технической документации не предусмотрена зависимость изменения процента межлекальных отходов от числа комплектов лекал и конфигурации раскраиваемых деталей. Например, нормативы межлекальных отходов на корсетные изделия (бюстгальтеры) классифицированы по основным конструктивным формам изделий и видам тканей с учетом 10—20 комплектов лекал в раскладках.
Работниками ЦНИИШПа предложен новый способ построения плотных многокомплектных раскладок лекал— ЛОГ-способ. В основе ЛОГ-способа лежит идея локально-оптимального группирования деталей, близких па геометрической конфигурации и размерам; нахождения последовательности таких предпочтительных чисел, выбор которых обеспечивает монотонное снижение межлекальных отходов с увеличением числа комплектов лекал; установления оптимальной структуры раскладки.
Этот способ был подробно описан в ранее опубликованной статье (см. «Швейная промышленность», 1984,. № 6). Разработанная пошаговая процедура построения плотных многокомплектных раскладок лекал корсетных изделий и полученные устойчивые результаты снижения межлекальных отходов позволили разработать альбом уплотненных многокомплектных раскладок, которые значительно упрощают применение ЛОГ-способа на практике.
Впервые разработан способ сокращения межлекальных отходов для моделей, состоящих из двух — пяти деталей различной конфигурации и раскраиваемых из одного и того же материала (положительное решение no-заявке 3787488/28-12). Например, для четырех различных по конфигурации деталей существует 15 различных, вариантов компоновки гнезд раскладок как отдельных деталей, так и их сочетаний.
Существующим методом, т. е. интуитивно, определить, плотность каждого гнезда раскладки и выбрать оптимальный вариант даже опытный раскладчик не может. Реализация такой задачи на ЭВМ позволяет автоматизировать все необходимые расчеты и путем выбора оптимального варианта получить дополнительный «выигрыш»-не менее 1 % по сравнению с ЛОГ-способом.Указанные способы построения плотных раскладок лекал нашли практическое применение на корсетных изделиях, головных уборах, деталях мягкой игрушки, клиньях юбок и платьев, деталях прокладок пальто и костюмов,, кожгалантерейных изделиях и т.д.
Статья из архива журнала «Швейная промышленность» 01/1988 автор Герасимова Н.И.
Значительные отходы материалов в швейной промышленности, возникающие при раскрое изделий, обусловливают необходимость дальнейшего развития теории и практики нормирования материалов.
В результате исследований, проведенных в Челябинском филиале ЦНИИШПа. разработаны и внедрены три способа сокращения отходов материалов при раскрое изделий различного ассортимента: оптимизация числа комплектов лекал с учетом суммарных отходов; построение плотных многокомплектных раскладок лекал; адаптивное конструирование.
1. Оптимизация числа комплектов лекал в раскладках с учетом суммарных отходов
В швейной промышленности действует система норм и нормативов материальных ресурсов, представленных инструкциями по нормированию и рациональному использованию материалов и отходов производства. Обычно при разработке нормативно-технической документации, регламентирующей порядок рационального использования материалов, устанавливаются нормативы на отдельные составляющие отходов: межлекальные, маломерные остатки (мерный и весовой лоскут), по длине и ширине настилов за рамкой раскладки и т. д. Однако материалы используются тем рациональнее, чем меньше суммарные отходы [1].
Анализ материалоемкости швейных изделий позволил установить, что для достижения эффективности результатов в снижении суммарных отходов недостаточно обеспечить выполнение предприятием действующих нормативов по использованию материалов, т. е. отдельных составляющих отходов.
Соблюдение этих нормативов далеко не всегда означает, что рассмотрены и исчерпаны все возможности. Количество отходов существенно колеблется в зависимости от выбранного плана раскроя, и, кроме того, мероприятия, направленные на уменьшение одних отходов, зачастую вызывают увеличение других.В конечном итоге важна не структура отходов и величина их составляющих, а достижение максимального процента использования материалов.
Другой проблемой рационального использования материалов можно считать проблему качества текстильных материалов. Наличие текстильных пороков в материалах ведет к увеличению числа разрезаний кусков (для размещения дефектов в конце настила или на стыках полотен), увеличению количества маломерных остатков из-за вырезания брака, а также вызывает необходимость индивидуального раскроя полотен.В результате исследований, проведенных в Челябинском филиале ЦНИИШПа, было установлено, что доля шелковых тканей первого сорта, поставленных на швейные предприятия в 1981—1984 гг., составила 57—66%, причем эта доля ежегодно сокращалась в среднем на З%.
Затраты швейных предприятий на переработку тканей с текстильными пороками постоянно возрастают и в настоящее время составляют на каждое изделие (платье женское и детское, сорочка мужская и детская, корсетные изделия) в среднем 0,4% его оптовой цены. В объеме всей отрасли из-за низкого качества шелковых тканей швейники ежегодно теряют более 6 млн руб., причем для швейных предприятий эти потери невосполнимы, так как текстильные предприятия поставляют материалы по цене первого сорта независимо от их фактической сортности. Подобным образом обстоит дело и с качеством других тканей.В сложившейся ситуации швейные предприятия идут на уменьшение числа комплектов лекал в раскладках, а следовательно, и длины раскладок.
В Челябинском филиале ЦНИИШПа был разработан аналитический способ выбора оптимального числа комплектов лекал с учетом суммарных отходов. Сущность этого способа заключается в установлении диапазона оптимального числа комплектов лекал при условии минимизации суммарных отходов межлекальных и маломерных остатков.Математически поставленную задачу можно сформулировать следующим образом: с увеличением комплектности раскладки №, а следовательно, и длины раскладки количество межлекальных отходов А уменьшается, а количество маломерных остатков В увеличивается. Это означает, что существует оптимальное число комплектов лекал №, для которого количество суммарных отходов С минимально.
Для решения поставленной задачи были собраны соответствующие данные по количеству (проценту) межлекальных отходов и маломерных остатков в производственных швейных объединениях, специализирующихся на выпуске корсетных изделий: челябинском «Силуэт», московском «Черемушки», ленинградском «Трибуна» и др.Для аппроксимации процента указанных отходов А, В, С были выбраны следующие трехпараметрические функции [2]:
Для определения параметров эмпирических функций зависимости процента межлекальных отходов и маломерных остатков от числа комплектов лекал был использован метод наименьших квадратов.
Практически для вычисления процентов межлекальных отходов, маломерных остатков и суммарных отходов в зависимости от числа комплектов лекал корсетных изделий могут быть использованы следующие формулы: Для определения оптимального числа комплектов лекал в раскладках с учетом минимального количества суммарных отходов выполнены два варианта расчетов кусков тканей в настилы. В первом варианте расчеты выполнялись при монотонном возрастании числа комплектов лекал в раскладках, но при сохранении на одном уровне процента малокомплектных раскладок, во втором варианте расчеты выполнялись без указанного ограничения. В обоих случаях суммарные отходы определены в зависимости от изменения показателя среднего числа комплектов лекал.
Второй вариант расчета, используемый в промышленности, наиболее целесообразен, однако в этом случае диапазон оптимального числа комплектов лекал снижается до 15—19 (теоретическое значение №=27).
Реализуемое в настоящее время на практике среднее число комплектов равняется 10—12 (при условии, что все детали изделия раскраиваются из одного вида материала), а это значительно меньше оптимального числа комплектов.Использование оптимального числа комплектов лекал в раскладках при раскрое, например, корсетных изделий позволяет получить экономию ткани до 0,5—0,8%.
Такой подход к выбору оптимального числа комплектов лекал при раскрое головных уборов на Ташкентской фабрике головных уборов им. Ахунбабаева способствовал уменьшению суммарных отходов на 2,5%. Используемое на этом предприятии среднее число комплектов для выбранной модели составляло 29, а оптимальный диапазон, определенный в результате расчетов, составил 14—19 комплектов. На трикотажных предприятиях при раскрое трикотажных полотен для уменьшения маломерных остатков в раскладках лекал предусматривают секции. При этом количество секций в раскладках устанавливается произвольно: 4—6 секций в одной раскладке изделий для взрослых и до 13 секций — в одной раскладке изделий для детей. Оптимизация числа секций в раскладках лекал при раскрое трикотажных спортивных костюмов позволяет уменьшить суммарные отходы на 0,3—4,8'%.Статья из архива журнала «Швейная промышленность» 01/1988 автор Герасимова Н.И.